This article features takeaways from our recent webinar on embracing lean across all functions of an organisation. You can watch the webinar recording on-demand – right here.
Efficiency and continuous improvement are not just goals; they are necessities for organizational survival. The principles of lean have transcended their manufacturing origins to become vital across all business functions. The concept of lean, often associated with the pioneering Toyota Production System, is a comprehensive approach focused on maximizing value through the elimination of waste and optimization of processes and resources.
However, embracing lean principles is not limited to production floors or the frontline. It is equally crucial in every corner of an organization; from HR to Finance, Marketing to R&D – all the way to the boardroom.
The Essence of Lean: A Dual Focus on Process and People
Lean methodology is built on two foundational elements: efficient processes and the empowerment of people.
The iconic Toyota house model encapsulates this philosophy, presenting an ambition to achieve the lowest cost, highest quality, and shortest lead time. These goals are supported by a framework that emphasizes flawless products and waste-free processes.

However, lean is not just about processes; it is equally about people.
The Toyota Way, with its emphasis on respect and continuous improvement, underlines the importance of a culture where every employee is engaged in the pursuit of perfection.
Embracing Lean Universally
Lean methodology’s principles are universally applicable across all organizational functions. The traditional equation of cost plus profit equalling price is inverted in a lean organization.
Instead – by starting with the market price and subtracting cost – companies focus on cost reduction as a pathway to profit improvement. This approach necessitates a collaborative effort across all functions to identify and eliminate waste, thereby enhancing value.
It helps to frame this thinking with the following mantra:
“Every function has a customer”
When you do so, you create a universal starting point for improvement cycles. By keeping things ‘customer-centric’ – focused on the end of the value chain – functions can identify an ideal state to work back from.

Consider some of the most-recognisable enterprise organisations in the world and their customer value propositions. With these laid out, many of the organisations choices / processes – product or service design, org structure, marketing, even geographic presence – make a logical, clear sense.

These organisations have clearly defined their customer value which then cascades into each function. Enabling them to embrace Lean and effectively follow the best practice cycle – keeping the following top-of-mind:
- Who is your customer?
- What value is delivered?
- What does perfection mean?
Here’s TeamAssurance’s CEO, Matt Mafrici, working through a practical example of this:
Cost, Quality, and Lead Time: The Triad of Lean Focus
As you can see the lean approach to management and operations is distinguished by its meticulous focus on three fundamental areas: cost reduction, quality enhancement, and lead time minimization. This triad forms the core of lean’s promise to transform organizations into more efficient, responsive, and customer-focused entities.
- Cost Reduction:
Lean practices dive deep into analyzing and reducing costs without compromising the quality or value delivered.
Cost reduction transcends doesn’t simply mean adhering to austerity measures but rather working towards overall organizational efficiency and competitiveness. By examining direct and indirect materials, labor, and other overheads, lean seeks to streamline operations and reduce unnecessary expenditures.
For example: excess inventory, overproduction, unnecessary process steps, time waste and excess labour. - Quality Enhancement:
Quality is not merely an output metric within the Lean framework; it is a fundamental principle that permeates every aspect of operations and decision-making. Lean methodologies champion a data-driven approach to quality improvement, emphasizing the importance of understanding customer needs and expectations deeply.
It elevates product and service quality and often involves cross-functional collaboration to identify root causes of issues and implement lasting solutions.
By breaking down silos and encouraging teams from various departments to work together, organizations can more effectively identify the root causes of quality issues. Techniques such as the Five Whys and fishbone diagrams facilitate a deeper analysis of problems, leading to more sustainable solutions.
Through continuous improvement cycles, companies can elevate their product and service quality, fostering loyalty and trust among their customers. - Lead Time Minimization:
Contrary to filling warehouses to ensure prompt delivery, lean focuses on reducing the time from production to delivery. This exposes deep-seated inefficiencies and waste, forcing organizations to confront and rectify these issues. It fosters a more robust and efficient operation.
Reducing lead time not only requires a thorough examination of the production process but also a commitment to solving the problems that slow it down. This can involve re-engineering processes, adopting just-in-time production methods, and enhancing coordination between different parts of the organization.
The benefits of embracing Lean for lead time minimization are substantial, leading to increased flexibility, reduced inventory costs, and the ability to respond more swiftly to market changes and customer demands.
Leveraging Technology in Lean Transformations

Technology plays a pivotal role in embedding lean capabilities within an organization. By distinguishing between human and machine work, technology enhances efficiency, reduces barriers to standard work practices, and fosters an environment of continuous improvement. Examples include:
- Lean Strategy Deployment:
The deployment of lean strategies across an organization requires a seamless connection between high-level strategic goals and day-to-day operational activities. Technology plays a crucial role in this process by providing platforms that can break down business strategies into actionable tasks, distribute these tasks across the organization, and track progress in real-time.
It ensures that every function is not just busy, but aligned with the organizational goals. It moves the needle on critical success metrics and driving tangible progress towards the vision.
For example, digital lean management systems can visualize workflows and activity under management. This allows teams to see how their efforts contribute to larger objectives and continuously promotes a culture of accountability and CI.
- Lean Standard Work Processes:
The heart of lean is in its standard work processes—repetitive patterns of activity that ensure efficiency and quality. However, maintaining the relevance of these standards in a rapidly changing environment can be challenging. Technology provides a dynamic solution to this problem by making standard work processes easily accessible, understandable, and modifiable.
Digital tools and platforms can house an organization’s entire repository of standard operation procedures (SOPs), making it easy for employees to access up-to-date instructions and guidelines. More importantly, these platforms can facilitate real-time updates and improvements to standard processes, allowing organizations to adapt quickly to new information or changing conditions.
Embracing lean embeds a dynamic approach to standardization. One that ensures processes remain relevant, employees stay informed, and the organization retains its agility.
- Routine Work Processes:
The application of technology in streamlining these processes is transformative for day-to-day, week-by-week processes. Daily checklists, structured meetings and monthly reports, form the backbone of any organization’s operations.
Tech enables the automation of mundane tasks, accurate data capture and analysis, elimination of human error and the provision of actionable insights through real-time analytics.
Teams gain immediate and open feedback on their performance against key metrics. This capability enables organizations to make swift adjustments, address inefficiencies, and capitalize on opportunities for improvement as they arise.
Furthermore, removing administrative burden frees up employees to focus on higher-value activities that require human creativity and judgement. -
Embracing Lean Across the Organization
To truly embed lean, organizations must integrate it into their very fabric, ensuring that processes, people, and technology work in harmony. This holistic approach requires a commitment to continuous improvement, cross-functional collaboration, and a culture that values excellence and efficiency.
By focusing on the unique value each function brings and leveraging technology to facilitate lean practices, organizations can create a sustainable competitive advantage.
Lean is not solely a set of tools or methodologies. It is also a mindset that must permeate every level of an organization. Its principles are as applicable in the boardroom as they are on the production floor, offering a path to excellence that transcends industry boundaries.
By embracing lean, organizations can not only improve their operational efficiency but also foster a culture of continuous improvement that drives long-term success.
Embracing Lean Within Every Process of Your C.I. Framework
To ensure a synergistic, cohesive effort across all areas of strategy, project and daily management, we must ensure that each is built with all adjacent areas (and their respective processes) in mind. For example, daily routines like Leader Standard Work and Daily Huddles must be supported by standardised problem solving techniques, documentation and a disciplined PDCA process.
Comme nous l'avons mentionné plus haut, pour parvenir à cette cohésion, aucun élément du cadre C.I. élargi ne doit être orphelin ou développé de manière isolée. C'est pourquoi nous avons conçu une plateforme interconnectée qui garantit l'absence de "solutions ponctuelles" déconnectées (numériques ou analogiques) susceptibles d'empêcher les organisations d'atteindre leurs objectifs.
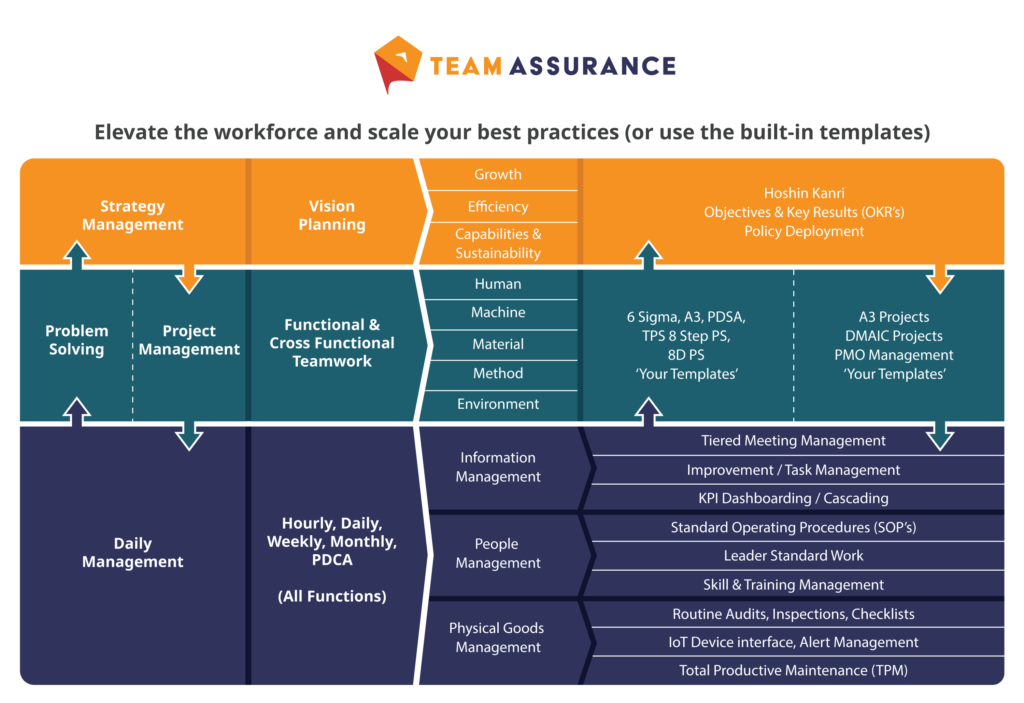
If you are a business in need, or a Consultant with clients looking for support, contact us for a live demonstration of TeamAssurance.